针对工业风机在变工况(如流量突变)下的稳定性问题,通过主动控制策略改善需结合动态响应分析、先进控制算法和系统集成技术。以下是系统性解决方案:
1. 问题分析与控制目标
1.1 变工况不稳定的根源
- 流量突变影响:
- 气动载荷波动 → 叶片失速/喘振 → 效率骤降、振动加剧
- 惯性延迟 → 电机-叶轮转速失配 → 扭矩振荡
- 典型场景:
- 钢铁厂除尘系统阀门突然开闭
- 化工流程中反应釜压力骤变导致的排气需求变化
1.2 控制目标
- 核心指标:
- 响应时间 <100ms(避免喘振)
- 转速波动幅度 <±2%额定值
- 静压恢复时间 <1s
2. 主动控制策略设计
2.1 传感器网络配置
- 关键监测参数:
- 实时流量(超声波流量计)
- 进出口压力(差压变送器)
- 转速(编码器)
- 振动(加速度计)
- 数据融合:
- 卡尔曼滤波消除噪声,提升信号可靠性
2.2 控制算法选择
- 经典PID改进:
- 模糊自适应PID:根据误差变化率动态调整参数(如Kp随流量偏差非线性变化)
- 抗积分饱和PID:限制积分项累积,避免超调
- 现代控制方法:
- 模型预测控制(MPC):
- 建立风机状态空间模型,滚动优化未来3-5步控制量
- 处理流量突变的多变量耦合(如转速、压力、温度)
- 滑模控制(SMC):
- 设计滑模面强制系统状态快速收敛,鲁棒性强
- 需解决高频抖振问题(可用饱和函数替代符号函数)
- 模型预测控制(MPC):
2.3 执行机构响应
- 变频调速(VFD):
- 选用矢量控制变频器(如ABB ACS880),转矩响应时间 <10ms
- 导叶调节:
- 前导叶动态角度补偿(与变频协同控制)
- 喘振保护:
- 快速泄压阀(电磁阀动作时间 <50ms)
3. 系统实现与验证
3.1 数字孪生仿真
- 模型构建:
- 1D-3D耦合模型(如GT-Suite+ANSYS Fluent)
- 模拟流量阶跃突变下的瞬态流场
- 硬件在环(HIL)测试:
- dSPACE平台实时验证控制算法
3.2 现场调试
- 阶跃响应测试:
- 突增/突减30%流量,记录压力-转速曲线
- 抗干扰测试:
- 人为引入电网电压波动(±10%),观察系统恢复能力
4. 典型案例与效果
4.1 某水泥厂窑尾风机改造
- 问题:生料投料波动导致风机频繁喘振
- 方案:
- 采用MPC+前馈补偿(投料信号提前触发转速调整)
- 加装高频压力传感器(采样率1kHz)
- 效果:
- 喘振次数降为0,电耗降低8%
4.2 石化行业丙烯压缩机
- 问题:紧急停机时回流阀开启引发喘振
- 方案:
- 滑模控制快速调节导叶,配合泄压阀联锁
- 效果:
- 压力波动幅度减少70%
5. 关键技术挑战与对策
- 挑战1:模型精度不足
- 对策:在线参数辨识(递归最小二乘法更新模型)
- 挑战2:执行机构延迟
- 对策:时间延迟补偿(Smith预估器)
- 挑战3:多机协同
- 对策:分布式模型预测控制(DMPC)协调多台风机组
6. 未来方向
- 数字孪生+AI:
- LSTM神经网络预测流量突变趋势,提前触发控制
- 新型作动器:
- 压电陶瓷驱动导叶,响应速度提升至μs级
实施流程图
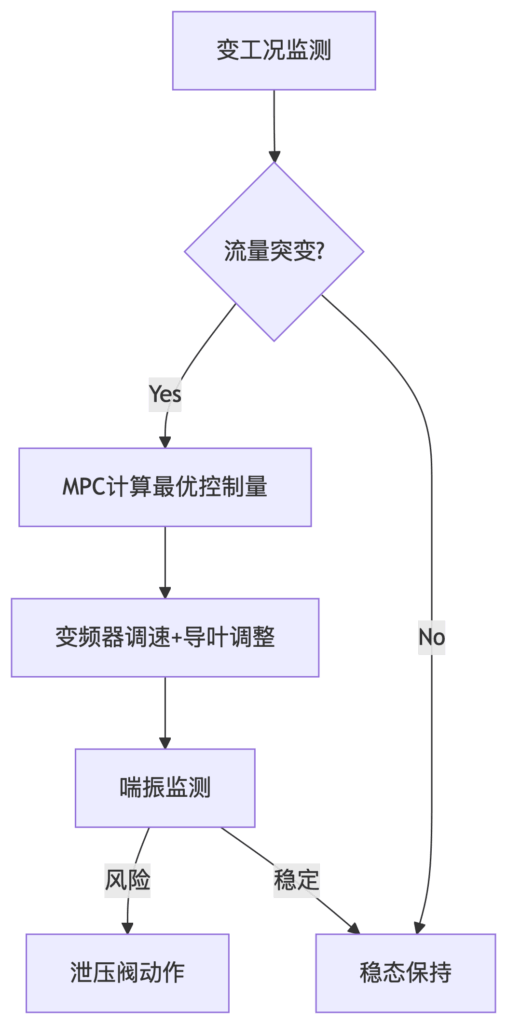
通过上述主动控制策略,工业风机可在变工况下实现快速稳定,显著降低故障率并延长设备寿命。实际应用中需根据具体风机类型(离心/轴流)和工艺特点定制控制逻辑。